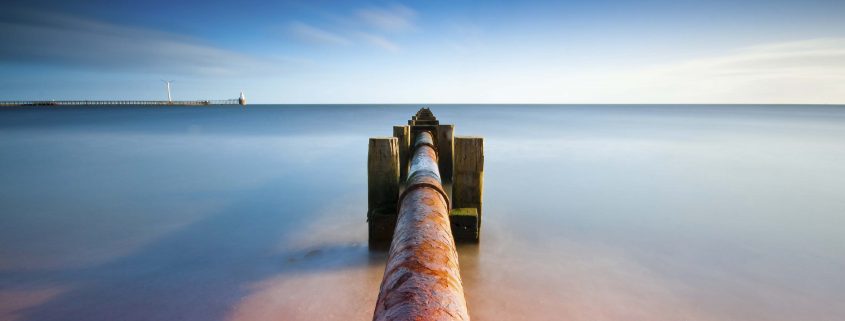
Micro-Tunneling
Pipe-jacking and Microtunneling are relatively recent technology advancements in underground engineering. As such, it is sometimes difficult to locate experienced engineering professionals in these areas. However, SubTerra has both in-house resources and the ability to utilize its network of professionals to provide expertise in these areas.
Microtunneling, which is a special case of pipe-jacking, was first developed in Europe and Japan and was not used in the U.S. until the mid 1980s. Microtunneling is defined in the U.S. as a remotely controlled, laser-guided pipe-jacking process that does not require personnel entry for the excavation and mucking process. Since the process can be used to install a wide range of pipe sizes (limited only by the practical consideration of the jacking thrust required to overcome frictional resistance of large surface area pipe), artificial size constraints do not technically factor into the definition of microtunneling. However, the most common applications of microtunneling methods typically involve “no-man entry”, or small diameter tunnels, hence the name.
Pipe-jacking techniques in the U.S. were developed primarily in the Midwest states in the 1970s and early 1980s. As the name suggests, the method involves jacking a pipe or liner along the required alignment while excavating material at the face formed at the leading edge of the pipe. Virtually any mining technique can be used to advance a tunnel using the pipe-jacking technique. The primary difference between pipe-jacking and conventional tunneling techniques is in the method used to install the lining.
Pipe-jacking (and in the right conditions, microtunneling) can potentially be a cost saving alternative to deep open-cut excavation and conventional tunneling methods. There are also obvious advantages with these methods over open-cut excavation where surface disturbance is not permissible. Case histories have shown that intensive geotechnical and geological characterization of a project site is vital to the success of these methods, especially with regard to microtunneling.
Advantages & Disadvantages of Pipe-Jacking & Microtunneling
Pipe-Jacking Advantages
- Greatly reduced surface and shallow utility disruption
- Flexibility in excavation method and in handling unexpected or anomalous ground conditions
- Eliminates need for two-step liner (i.e. initial support)
- Typically reduced or eliminated seepage into completed section of tunnel
Pipe-Jacking Disadvantages
- Limited tunnel run resulting in more required shafts (approx. every 1000 ft)
- Relatively straight alignment required
- Difficulty replacing damaged pipe
Advantages of Microtunneling (in addition to Pipe-Jacking)
- Remote excavation and mucking of small diameter (“no-man” entry) tunnels
- Increased safety to workers
Disadvantages of Microtunneling
- Limited options if unexpected conditions encountered resulting in machine stoppage (i.e. rescue shaft)
- Difficulty in maintaining line and grade if obstructions encountered
Preliminary Investigations
Preliminary Investigations to identify critical engineering and geotechnical issues associated with overall project feasibility and potential application of pipe-jacking or microtunneling methods, defining design information needs, and providing preliminary cost estimates for excavation alternatives
Design and Implementation of Site Investigation Programs
Design and Implementation of Site Investigation Programs, for new tunnels, focused to project specific geotechnical issues and design information needs, including:
- Site reconnaissance and mapping
- Layout and supervision of exploration plans
- Identification of laboratory and in-situ testing needs
- Instrumentation setup and monitoring
Interpretation of Site Investigation Data
Interpretation of Site Investigation Data to provide geological characterization and a geotechnical framework for excavation design, risk assessment, and preparation of factual and interpretive reports.
Design and Engineering Services
Design and Engineering Services:
- Excavation method selection, including risk-based modeling of excavation system performance
- Review of contractor proposals
- Blast design, monitoring and optimization
- Design of ground support and monitoring systems including design with shotcrete, geotechnical instrumentation for support performance verification
- Seepage estimation and control
- Subsidence evaluation and monitoring
- Ventilation system design and surveys
- Tunnel refurbishment/water proofing design and specification
- Geotechnical Data Reports (GDR)
- Geotechnical Baseline Reports (GBR)
- Project planning, cost and schedule estimates, Design Drawings, Specification and Bid Document preparation.
Field Services During Construction
Field Services During Construction, including:
- Geologic and geotechnical mapping of excavations
- Monitoring of geotechnical instrumentation
- Review of geotechnical data, stability analyses, and support design
- Monitoring of excavation progress with respect to geotechnical conditions
- Monitoring of support design with respect to conditions encountered
- Construction management and quality assurance
- Assessment of contractual claims related to ground conditions
- Change Order evaluation and negotiation
SubTerra, Inc. brings over twenty five (25) years of experience on over 100 completed Tunnel and Microtunnel projects. This experience includes Owner and Contractor Design, Design Review, Construction Management, Claims and Claims Management and Expert Support in Litigation. Projects include Conventional Excavation (drill-and-blast), NATM/SEM, TBM, EPBM, MTBM and a wide range of Pipe Jacking with tunnels as short as 40-ft and as long as 9-miles.
We specialize in Complex Designs providing simple solutions for Complex Projects using a full range of Design Tools and 3-D Modelling to demonstrate Complex Projects in advance of Construction.